Maintaining Optimal Temperatures: The Key Role Of Cooling Controllers In Food Storage
Cooling controllers are vital equipment that are used extensively in a variety of industries. This is because there are various applications and needs where temperature control is required. You may have heard of a PID controller containing control mechanisms that offer the best temperature control. These controllers operate heating or cooling mechanisms based on the current temperature and other factors. These factors tell the controller how intensely they should run the cooling or heating equipment to manipulate the temperature.
These cooling controllers are fundamental for food industry cooling solutions. The food industry requires precise temperatures. This is because temperature is the primary basis that affects the condition of food. This is why the optimal cool temperature must be achieved to ensure that food is preserved, whether it be through cooling or deep freezing. Cooling controllers can help control deep freezing technology to ensure the correct temperature is maintained and achieved efficiently. In this article, we will look at the critical role that cooling controllers play in food storage technologies. Let’s dive in.
Continuous Temperature Sensing
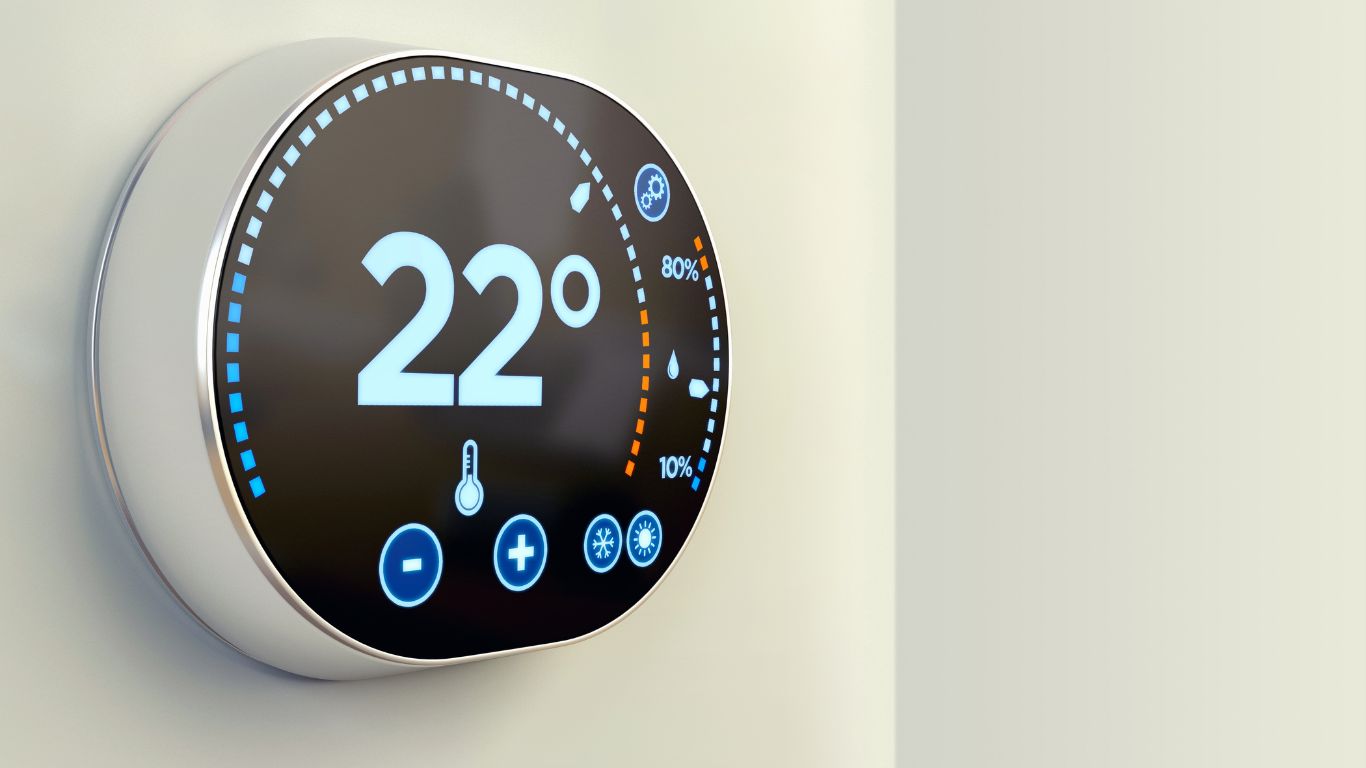
The temperature must be appropriately detected when it comes to cooling control solutions. As a result, cooling controllers work in tandem with temperature sensors to detect the temperature accurately. In essence, the sensors send continuous information about the current temperature to the cooling controllers so that they may achieve their functionality. Furthermore, these sensors are arranged to ensure that the data the controller uses is accurate and continuous. Therefore, sensors may be kept in different parts of the area or appliance. For example, consider deep freezing technology in a large walk-in fridge. Sensors would be placed in various sections and compartments to ensure that cooling controllers get accurate data so that they may be able to maintain optimal temperatures with the deep freezing mechanisms.
Achieving Temperature Set By Users
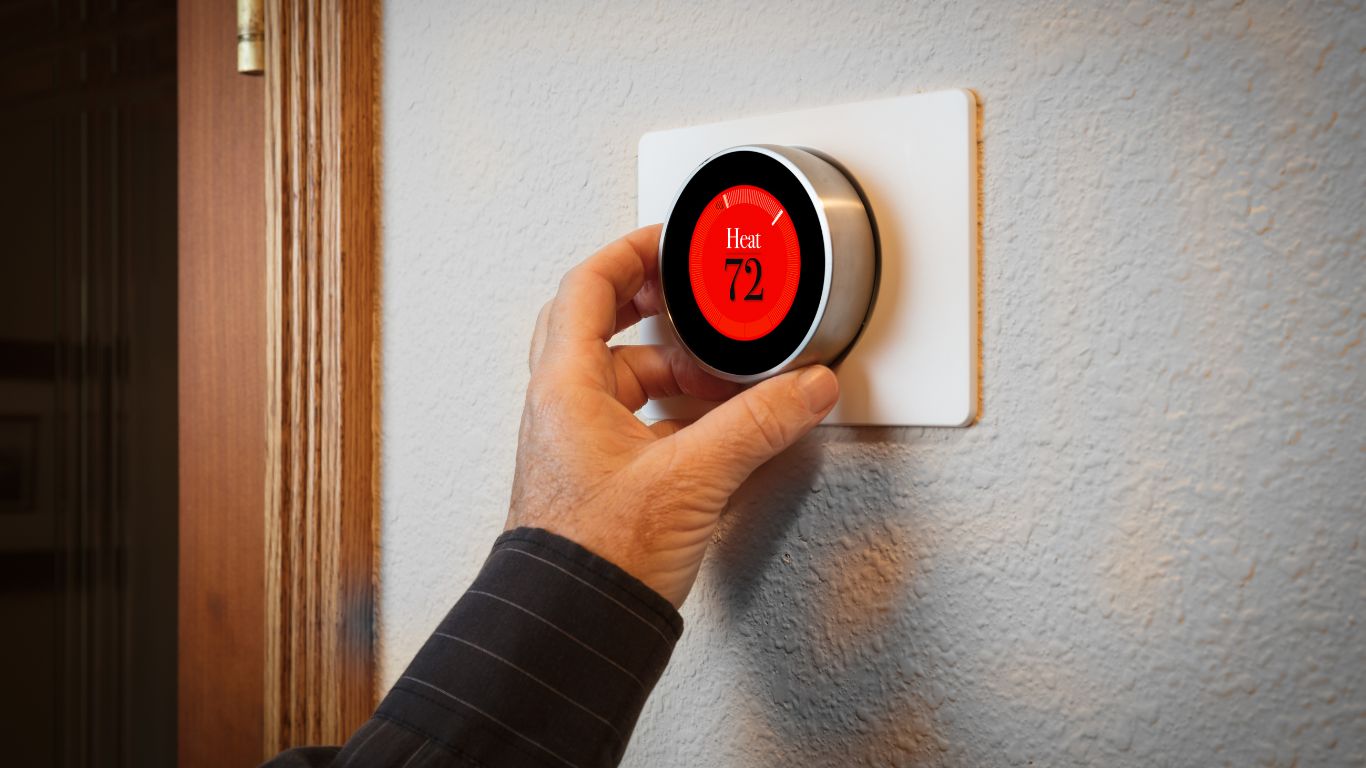
The experts and professionals within the food storage industry have knowledge and expertise regarding storing food at the right temperature. As a result, they will know what temperature should be set when operating appliances and food storage solutions. Whether the food needs to be cooled or frozen, these solutions must provide the option for these professionals to set the temperature. Typically, these professionals require precise temperatures to be maintained. This ensures the food is in the best condition, which is crucial for restaurants and culinary applications. After all, the food industry is competitive, and it is essential to maintain food in its best condition. However, retaining the temperature within these storage solutions is a complex task, especially when different compartments within an appliance need to be kept at different temperatures. This is where cooling controllers are essential, as they provide the functionality required to maintain these temperatures accurately. This is courtesy of the control mechanisms within these temperature control systems.
Temperature Adjustments
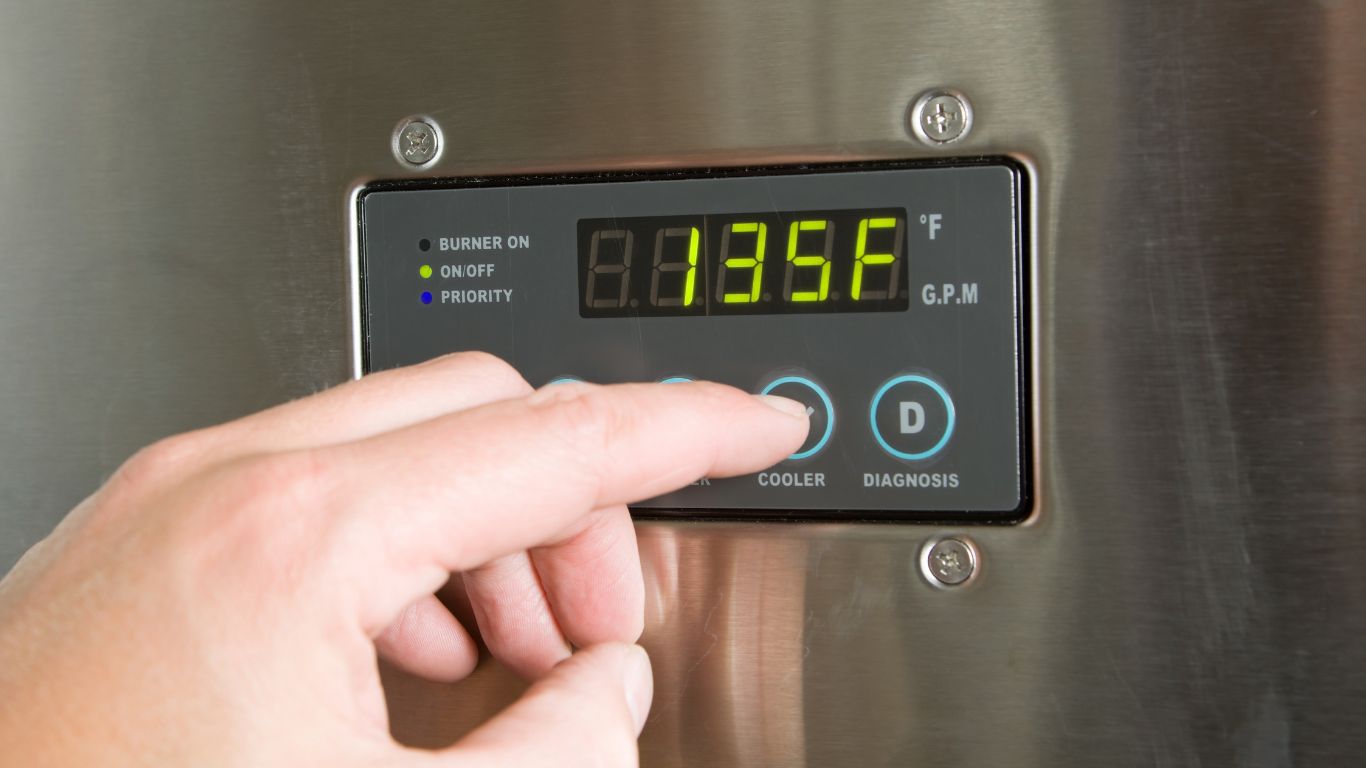
Cooling controllers must maintain the temperature, which means they must make regular adjustments when operating cooling and deep freezing mechanisms. In simpler terms, these cooling controllers must activate the cooling when the temperature rises too much and turn it off when it is too low. However, this simple process is inefficient and inaccurate leading to cooling controller challenges. This is where the control mechanisms that cooling controllers come equipped with come into play. These advanced control mechanisms examine how various variables differ from the desired value. These mechanisms work in tandem to ensure proper adjustments are made based on multiple recorded comparisons and values. Furthermore, these adjustments are made in real time as the controller monitors the temperature. As a result, optimal temperatures are maintained within food storage solutions.
Advanced Algorithms
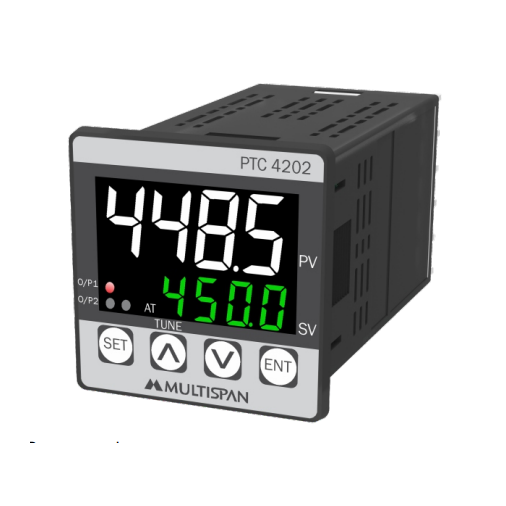
The control mechanisms that operate cooling controllers are complex as they compare the current and desired value of various variables and parameters. This is why they make use of P, I, and D algorithms that make use of the monitored data in a variety of ways. This is why cooling controllers are also sometimes referred to as PID controllers. The Proportional (P) control algorithm measures the difference between the actual and desired value of temperature. This difference is multiplied by a constant to produce an error to reduce the difference between the two values. The Integral (I) control algorithm documents the history of differences, temperature data, and door opening and uses this to adapt accordingly. If needed, ioT-enabled cooling controllers may connect to the internet to include weather data in their calculations. The Derivative (D) control algorithm measures the rate of change between the actual and desired temperature value. This ensures that the cooling mechanisms do not quickly cool the storage area. As a result, the controller can reduce the cooling power when it detects that the current temperature is closer to the desired setpoint. This ensures that the optimal temperatures are obtained and maintained.
Energy Efficiency
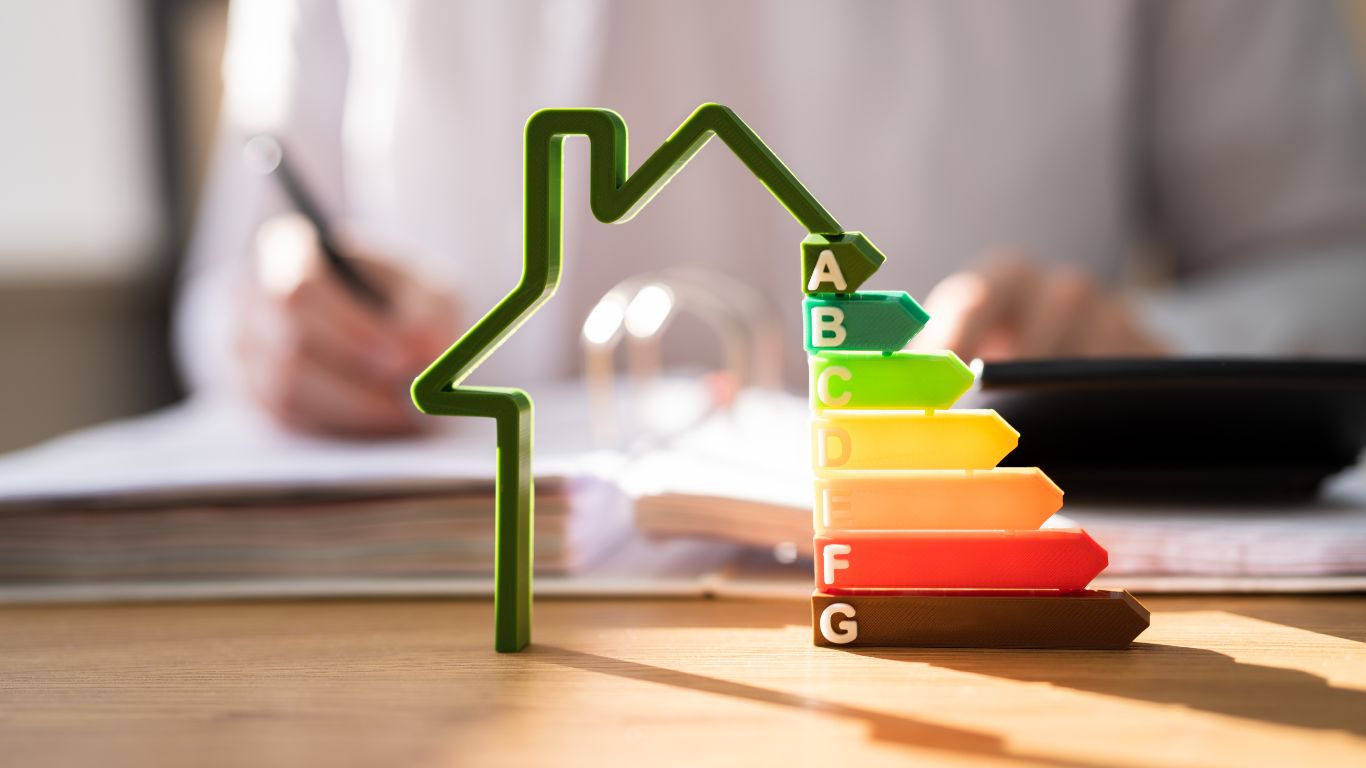
Food industry cooling solutions can be very intensive as these tend to be on an industrial scale. This means that a lot of food is stored within them. Furthermore, the temperature must be kept at the right temperature. Such cooling can take a toll on the systems, so ensuring the processes are as energy-efficient as possible is essential. The control mechanisms and algorithms mentioned previously ensure the cooling controllers can operate the cooling equipment in food storage solutions as efficiently as possible. This is because they reduce the number of times the equipment needs to be turned off and how fast it cools. Typically, with standard on-off controllers, this would be an inefficient process. As a result, there is less energy wastage which puts less stress on the systems while ensuring energy savings for users in the food industry. This is the case for both a digital and analog PID controller.
Defrosting Process
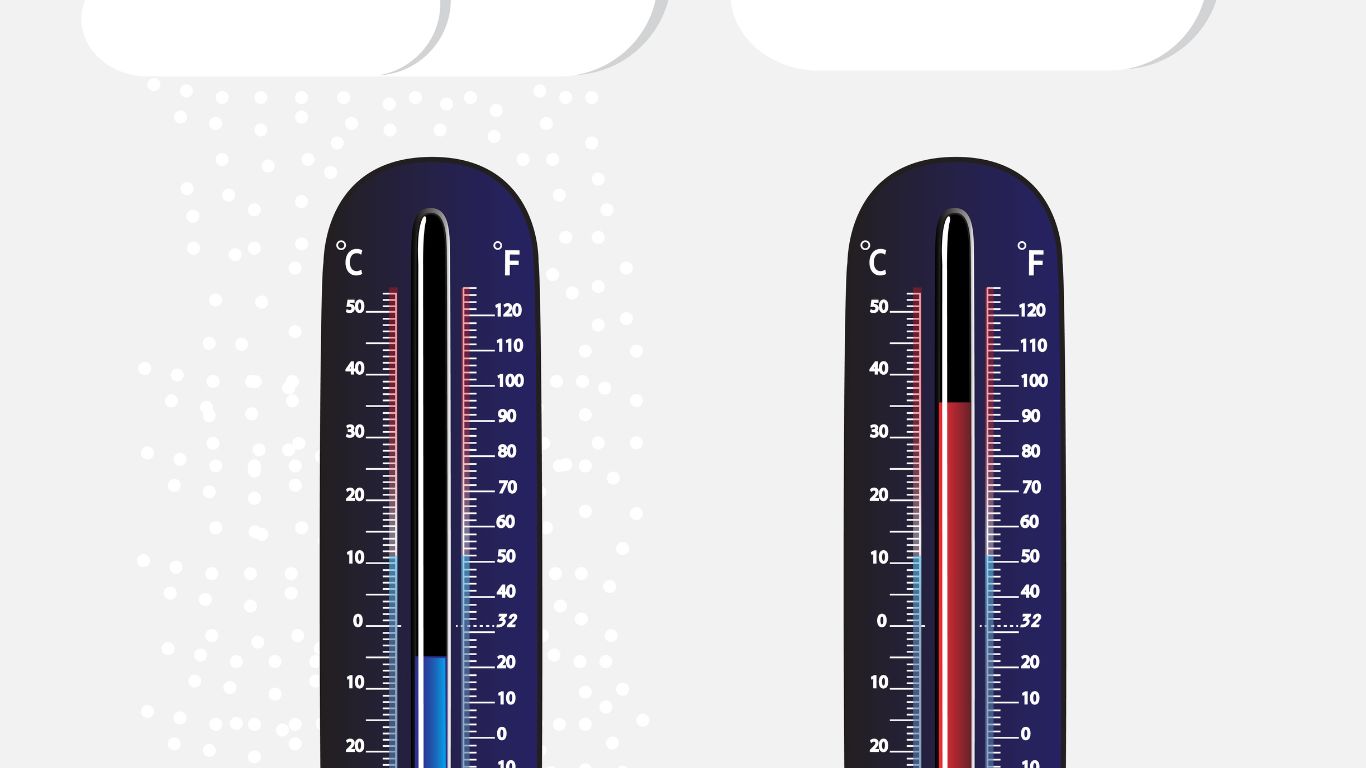
Deep freezing commonly uses cooling controllers for the entire process. However, there may be moments when the frost on the food builds up too much during deep freezing. On these occasions, the user may want to defrost the food so that they may prepare it for cooking or serving. For this purpose, the cooling controller can play a vital role. It can monitor the temperature to detect frost buildup on the food and then activate the defrost cycle. This is done by turning off the cooling, activating the heating equipment, and letting the frost melt. This process is done with continuous monitoring and calculations by the cooling controllers. The cooling controllers continuously make adjustments to ensure that the heating does not get too intense. This is because if the heat is too much, it can affect the food. This way, the ice melts gradually. After all, the purpose is to melt the frost and do this progressively and efficiently. In this way, cooling controllers can defrost the food stored efficiently.
The bottom line
Cooling controllers are vital equipment for the food storage industry. This is because food is a perishable item that needs to be at the optimal temperature. Otherwise, it can spoil. Cooling controllers help ensure that cooling and deep freezing technology keep the temperature at the desired point. They help measure and monitor the temperature with sensors in real time. After that, they maintain this set point by controlling cooling mechanisms like compressors. Since they measure temperature continuously, they adjust accordingly to ensure it does not deviate. They do so by using advanced algorithms that ensure the temperature is maintained efficiently and accurately. Finally, if there is too much frost buildup, cooling controllers can also be used for defrosting.
We hope this article has been insightful and helped you understand the key role of cooling controllers in maintaining optimal temperatures in food storage. Thank you for reading!
Leave a Reply