Maximizing Energy Efficiency: The Role of Analog and Digital PID Controllers
Extensive electrical processes occur within large complex systems and machinery in industries. These processes consume a lot of energy and electricity, leading to rising costs for the owners for whom cost-saving is essential to continue providing ideal products and services. Furthermore, inefficient energy processes can take a toll on the systems themselves. After all, much more heat and friction are created when processes go on longer than they should, leading to more maintenance and repairs. Many energy processes are required throughout the day. Some examples include process and temperature control. As a result, companies need to maximize their energy efficiency to ensure lower costs and better operation.
There are many energy management solutions and devices that are available. This article will discuss PID controllers, which effectively ensure maximum energy efficiency. We will examine the roles of both analog and digital PID controllers to understand which one you can use for your processes. Let’s dive in.
What are PID Controllers?
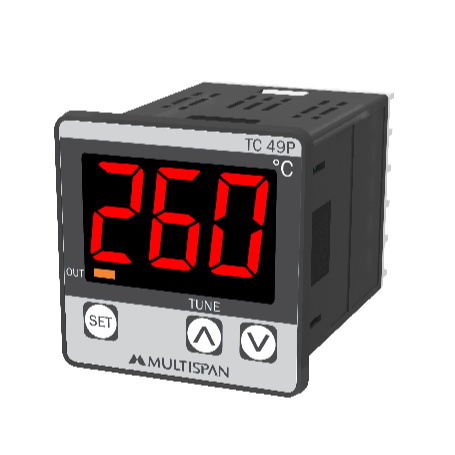
PID controllers can be described as control mechanisms that maximize energy efficiency and optimize the performance inside machines and systems. These control mechanisms can exist in the form of both hardware components and software algorithms. The type of PID controller you will use will depend on the PID controller applications. In this article, we will focus more on physical devices commonly used in industrial applications.
PID controllers are characterized by the three control mechanisms that it performs. These are the Proportional, Integral, and Derivative, which form the name for the controller, PID. These control mechanisms each have their algorithm, which the controller combines when it monitors machinery and systems. In essence, each mechanism involves the controller comparing a system variable with a desired value. The controller then manipulates the system until it is performing to fulfill that expected value. For example, if the temperature is too high, a PID temperature controller will operate the cool air to reduce the temperature.
PID Control Mechanisms
We will briefly touch on the control mechanisms used in PID controllers so you can understand how they maximize energy efficiency. These are:
Proportional Control (P)
The proportional controller gives an output that is proportional to the current error. This output is determined by comparing a set point to the actual value and multiplying this error with a set proportional constant. For example, if the error value is 2 and the proportional constant is 10, this would result in an output of 20. In essence, the purpose of this controller is to help reduce the difference between the actual and desired output. However, it can result in a steady state error that leads to the proportional constant increasing until the system becomes unstable.
Integral Control (I)
The integral controller gives an output based on the previous differences between the desired and actual values. The controller records the differences, in essence, documenting the history of differences. Based on the accumulated errors, the controller then adjusts the output. The purpose of doing so is to remove the steady state error that can occur due to the proportional controller.
Derivative Control (D)
The derivative controller gives an output based on the rate of change of the difference between the desired and actual value of a process variable allowing the controller to see how fast the different changes and adjust the output accordingly. For example, let’s consider a room that requires cooling through a PID temperature controller. If the difference is changing too quickly, this implies that the output is causing the setpoint to be rapidly achieved. As a result, the temperature might end up cooling beyond the desired value, resulting in inefficient energy management and overworking the cooling systems. However, the derivative controller can detect this rate of change and reduce the cooling as it approaches the setpoint. The derivative controller helps predict a system’s future error behavior.
Types of PID Controller
Analog PID Controllers
Analog PID controllers exist as physical devices that use analog electrical components. They were used extensively in industrial applications of the past before technology progressed and digital processes became more mainstream. They provide the main PID control feature we discussed above without additional components. However, they still offer some advantages.
Advantages
The advantages of analog PID controllers are:
Simplicity: Analog PID controllers have a reasonably simple design implemented within them, making them much easier to understand since no other complex processes are happening inside them. As a result, technicians will have a much easier time trying to fix them if an issue occurs.
Response Time: Analog PID controllers tend to have a faster real-time response time because the signal PID controllers deal with are analog, continuous signals. Digital PID controllers cannot understand these signals before converting them to digital. However, no such conversion is required with their analog counterparts.
Resilience: Analog PID controllers are much more resilient than their digital counterparts as the electrical processes within systems are continuous, analog signals. These signals can cause disturbance in digital components but not in the analog components of PID controllers. As a result, PID controllers are ideal for situations where there can be a lot of noise.
Low Cost: Analog PID controllers are much cheaper due to their simple design and lack of complexity. Furthermore, they have analog components, which are much more affordable. As a result, simple systems can use these energy-saving controllers without much trouble.
Digital PID Controllers
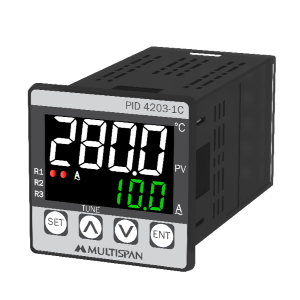
Digital PID Controllers can exist as devices and software algorithms and use PID control mechanisms in systems. You will also find much more complex components within them, like microprocessors or DSPs. These controllers take in digital signals and produce analog and digital output signals. Because of their advanced technology, digital PID controllers are much more prevalent now than their analog counterparts. They offer several distinct advantages and benefits.
Advantages
Flexibility: Digital PID controllers are much more flexible because they provide options like PID controller tuning, adjustments, and variable modifications. In this way, digital PID controllers can be used to adapt to changing demands and systems for an application.
Easier to Tune: PID controller tuning is essential for energy management solutions. It allows for better energy efficiency and integration that helps fulfill the needs. Digital PID controllers can be autotuned without the manual tuning required with analog controllers, which can be quite a hassle as systems must be opened.
Digital Integration: Digital systems and machinery have become more prevalent due to their advanced capabilities. For this purpose, digital PID controllers are ideal as they can seamlessly integrate with these systems and enable better features like data transfer and remote monitoring.
Advanced Features: Digital PID controllers can utilize more advanced algorithms than standard PID control mechanisms. By adding more algorithms, you can further boost the energy efficiency of your systems.
Data Storage and Analysis: Digital controllers provide the option of data logging and storage. Any data, like errors and processes, can be logged. Having this data on hand can be incredibly useful as it can be analyzed to help improve the algorithms for even better energy results.
In conclusion
PID controllers are convenient as they can help maximize energy efficiency courtesy of the PID algorithms within. These algorithms work hand in hand to ensure that the actual value is as close to the desired value as possible. PID controllers can be divided into two categories: analog and digital PID controllers. Each controller provides a distinct advantage that can change its role within advanced systems. We have gone through each of these so that you can understand exactly which one is ideal for your specific needs.
We hope this article has been insightful and helped you understand the role of analog and digital PID controllers in maximizing energy efficiency. Thank you for reading!
Leave a Reply